What is a Photopolymer Letterpress Plate?
by CLAIRE GREEN -
Here at Hoban Cards we use photopolymer plates for all our printing. If you've placed an order with us, you've probably noticed us talking about making your printing plate, or that we save your plate for future discounted reorders, but have you ever been curious about what exactly a photopolymer plate is? Read a bit further to learn more about this versatile printing matrix and how it's used at Hoban Cards.
Lead type, wood type, Linotype, woodblocks, copper plates, linocuts, and photopolymer plates. All these things can be printed in a letterpress, so why do we choose to work exclusively with the latter? Photopolymer plates are a new school material in an old school world. They bring versatility, convenience, and a wealth of design options to the print shop. With a little modification, any vintage letterpress can sport a photopolymer plate, bringing a touch of the 21st century to a Renaissance era technology.
A Little History...
The basics of letterpress printing were largely unchanged from the 15th century until the late 19th century. For hundreds of years, all printed matter, from books to newspapers to stationery, was printed from tiny pieces of metal type (and later wood type), each with a single letter, number or punctuation mark on it. Each piece of movable type was painstakingly set by hand to create a block of text by the compositor or typesetter. Once set, the type would be transferred to a press where it would be inked and pressed into a sheet of paper to create the print. By the late 1800's typesetting could be done mechanically using hot metal typesetting technologies such as Linotype or Monotype machines. Even though typesetting was much faster and easier to do than ever before, it was only a short time before letterpress was replaced by offset printing (which still reigns supreme today). Newspapers and book publishers sold off their letterpress equipment when switching to offset, and artists and craftspeople who wanted to revive the tradition of letterpress printing saved many of the old presses from destruction. Though most printers kept the tradition of handsetting their type, some wanted a more accessible way to print. Handset type requires a lot of space to store the physical type, which can be expensive to acquire and difficult to replace as metal type is easily damaged and worn. Enter photopolymer plates! In the 1980's printers discovered that light sensitive photopolymer could replace movable type. Instead of setting a block of text letter by letter, a single plate could be made directly from a digital file, and printed from that. This opened up letterpress printing to the digital world, allowing for much more freedom in the design process. For the first time, printers weren't limited by the amount of type they had in their shop, they now had access to digitally based typefaces and artwork!


Analog Meets Digital
What makes printing from photopolymer so unique is that it is born digital. A design is made on a computer using desktop publishing software and has all the benefits of the digital world: access to thousands of typefaces, the ability to easily add custom artwork such as logos, illustrations, or hand drawn lettering, as well as the ability to create and preview many design mockups without having to print each version. Once the details of the design are finalized, the plate is made and we enter back into the analog world of letterpress where the digitally made design is given life through ink, paper and pressure.
Ok, So What's a Photopolymer Plate?
Simply put, a photopolymer plate is a sheet of polymer with one side that is light sensitive. The digitally created design is transferred to a photo negative that is placed on top of the sheet of polymer. It is then exposed to light in a controlled exposing unit. The exposed areas harden and the rest stays soft and pliable. Then the plate is washed in water and rubbed with a soft brush (this is usually done in a dedicated washout unit, but can be done by hand too). The brush rubs away the soft unexposed material leaving behind only the areas that were exposed. After a final baking period to fully harden the plate material, it is ready to withstand the intense pressure of a letterpress!
In the world of letterpress, anything that needs to be printed, needs to be inked. To achieve this, a universal height of .918” is used. Whether printing on a small hand fed tabletop press or a huge fully automated press, .918 is the magic number. Photopolymer plates are much thinner than this and must be adhered to a specially made aluminum base that raises the plate to the exact height (called “type high”). The base is locked into the press bed where metal or wood type would traditionally be locked up for printing. Our plates have an adhesive back that allows them to simply stick to the base. The plate can be peeled away many times and stays sticky. (There are also metal backed plates that magnetize to their base, but we don't use those.) Once the plate is stuck to the base, it can be inked and printed (though there is a good deal of plate registration and adjusting of packing and ink application to get everything ready to finally print). We order large sheets of exposed photopolymer plates, with many jobs ganged up on the large plate. The plate material is soft enough to cut with a pair of scissors, so we hand cut individual plates from the larger one. Once printed, we store the plate where it waits for the day it might be reordered, and printed from again.

Why We Love Photopolymer
There are so many reasons to love photopolymer! Apart from the aforementioned convenience of digital typesetting and not needing to buy and store a literal ton of metal type, photopolymer is a really safe material to work with. Metal type is predominately made of lead, so care must be taken when working with it. Photopolymer on the other hand is quite inert and is very safe to handle. It's also lightweight and easy to store since the plates are so much thinner and lighter than traditional type high materials. We can fit a month's worth of jobs in a gallon ziplock bag, and a year's worth in a bankers box! When stored in a dark, airtight environment a plate can last several years. Photopolymer plates are also extremely durable – much stronger than metal type. This means that we can apply greater pressure when printing to achieve that ever desirable deep letterpress impression. (Fun fact: Did you know that letterpress printing with a deep impression was traditionally regarded as bad printing? It was only in the last couple decades during the letterpress revival that printing with an exaggerated impression became popular, most likely as a way to show off the uniquely tactile nature of letterpress compared to offset.) One last notable benefit of photopolymer is that it can’t be pied! Pied type is spilled type, and the bane of the typesetter. When typesetting and imposing, it’s very easy to knock over the neatly set type, often ruining many hours of diligent work and manifesting a few new gray hairs. Since this isn’t possible to do to photopolymer, the printer can avoid this particular source of anguish and get to printing faster!

We love the traditional aspects of letterpress printing and deeply appreciate the time and care that goes into working with metal and wood type. That being said, as a working shop, we prefer to leave the wood and metal to the fine press printers and hobbyists. Photopolymer plates allow tiny print shops like us the ability to offer a greater range of designs – and we are able to turnaround jobs faster and keep our cards as affordable as possible so that everyone can enjoy the beauty of letterpress!
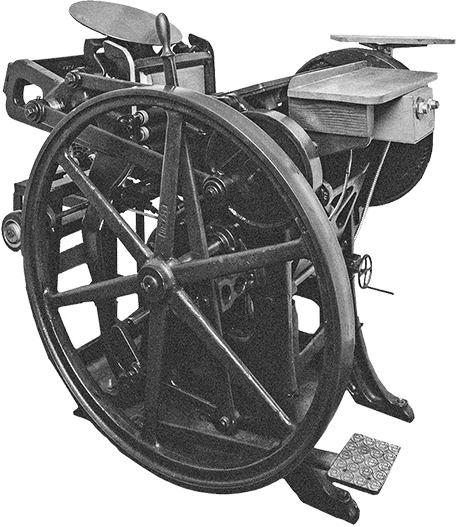
Thanks for Reading!
We not only love writing about letterpress, typography, and design – we're printers ourselves! We've chosen to carry on the tradition of letterpress printing by offering beautifully pre-designed cards at affordable prices.